How to make a carbide punch?
Making a carbide punch involves several steps and requires some specialized equipment and materials. First, we need to choose the right tungsten carbide material suitable for punching with durable use.
As a very hard and durable material, carbide is commonly used in stamping tools and press dies. There are various kinds of carbide models, for example, KD20, RD50, KX03, RG3, FD15, H40S and CD650 etc. Some are suitable for making square carbide punches like KD20, and some are suitable for machining round carbide punches, like H40S. There are also some common sayings for the carbide, like WC, or HM (abbreviation of “Hard Metal”).
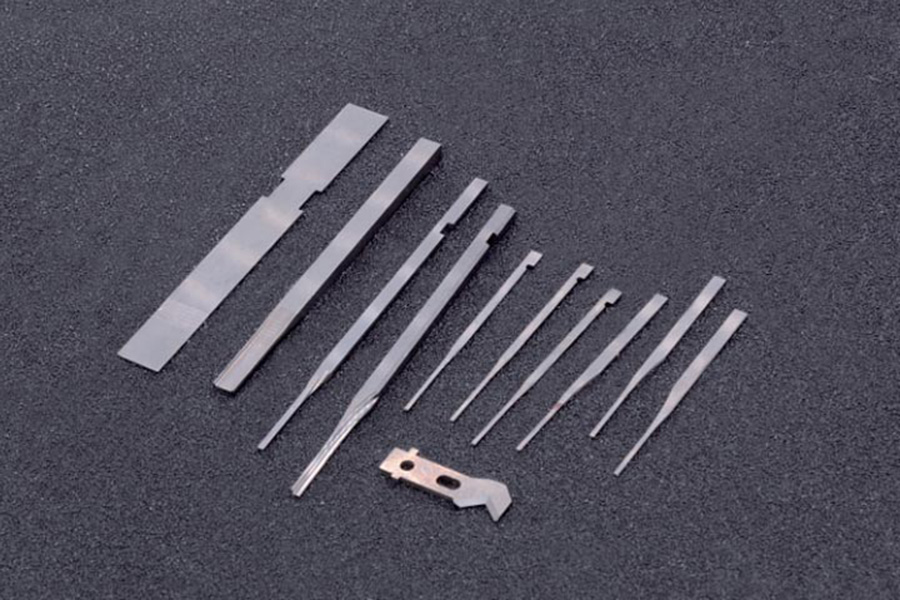
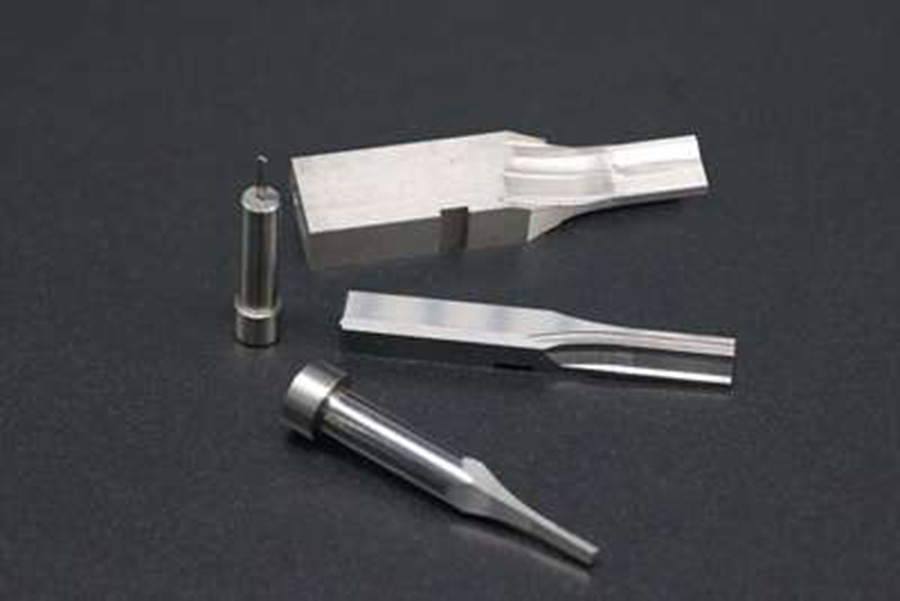
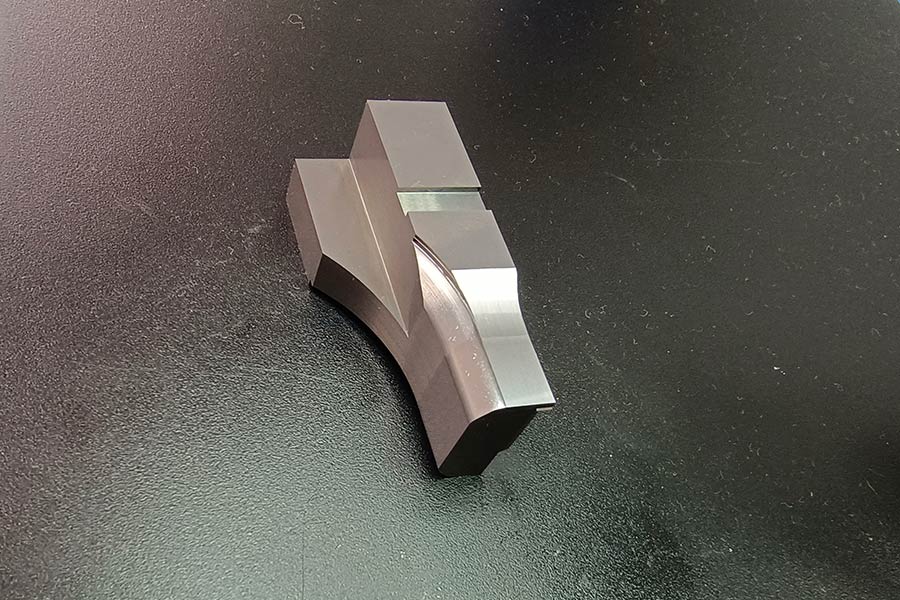
Here’s a general guideline of the process:
Design: According to the specific usage of a set of stamping dies, the mechanical designer determines the specifications and design of the carbide punch. This includes the dimensions, shape, and any specific features required for a specific application.
Material Selection: As we mentioned above, there are various kinds of tungsten carbide materials and models for selections for making carbide punches, some materials are made in Japan, some are made in Europe, and some are made in America or China. According to the punch shape(square, rectangular, or round), You’ll need to acquire tungsten carbide blanks in the appropriate size and shape for your punch.
Machining: Carbide is extremely hard and cannot be machined using traditional methods. Instead, it’s typically ground to shape using diamond grinding wheels or other abrasive methods.
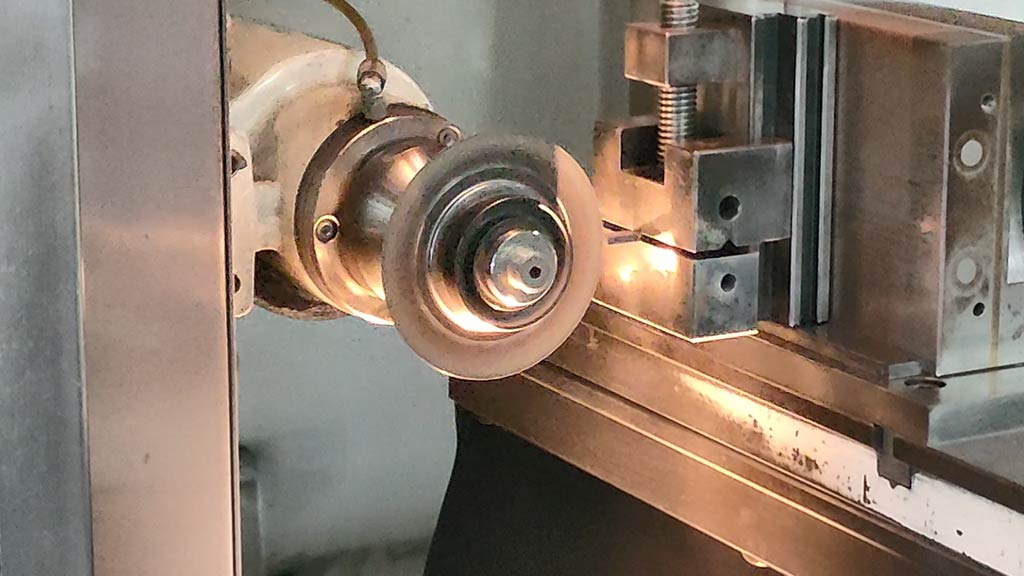
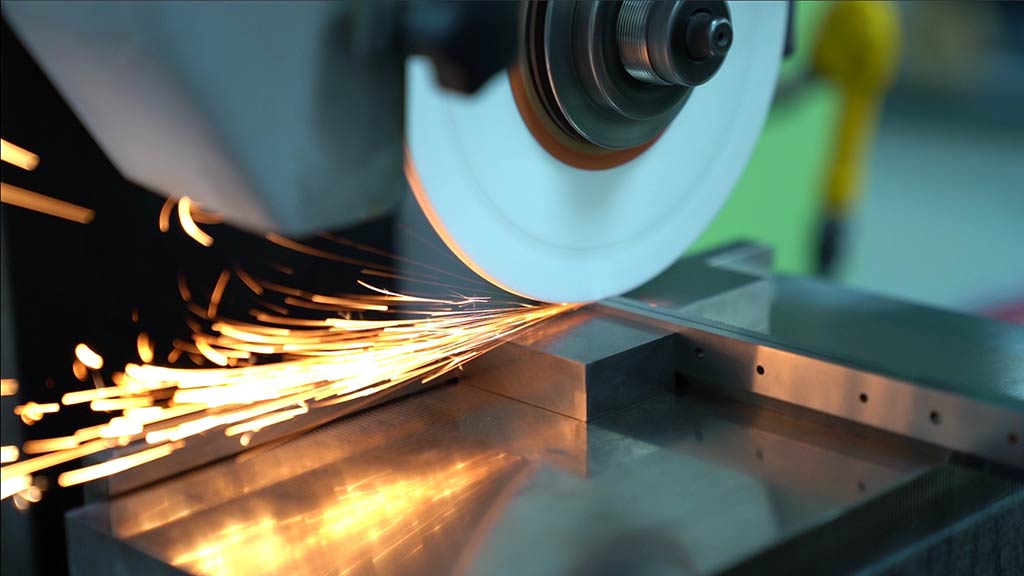
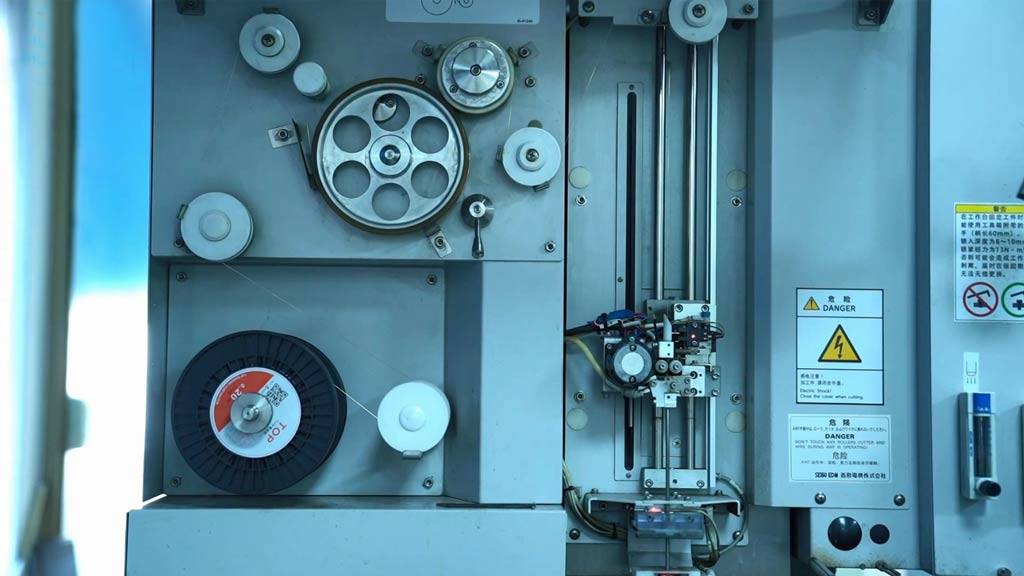
It also needs some special machining machines for making carbide punches, for example, profile grinding machine(PG), Plain Surface grinder with diamond grinding wheels(SG), wire-cut EDM machines, etc.
The wire-cut and Profile grinding may need to use CAD/CAM software to program the toolpaths and then can cut and grind the carbide punch to the desired shape and dimensions.
Finishing: After machining, the carbide punch may require additional finishing operations to achieve the desired RA surface finish. This can include high-glossy polishing or lapping processes for some specific areas.
Surface Treatment (Optional): Depending on the application, we may choose to apply surface treatments such as coatings or platings to further enhance the performance or durability of the carbide punch.
Some commonly used coatings for carbide punches or die inserts include DLC (abbreviation of “diamond-like carbon”), CrN, CrCN, Tin, TiCN, TiALN, TiALCN, AlCrN and AlCrTiN, etc.
Quality Control: Once the carbide punch is manufactured, it’s important to perform quality control checks to ensure that it meets the specified tolerances and performance requirements. This may involve dimensional inspection using precision measuring equipment and testing the punch under simulated operating conditions.

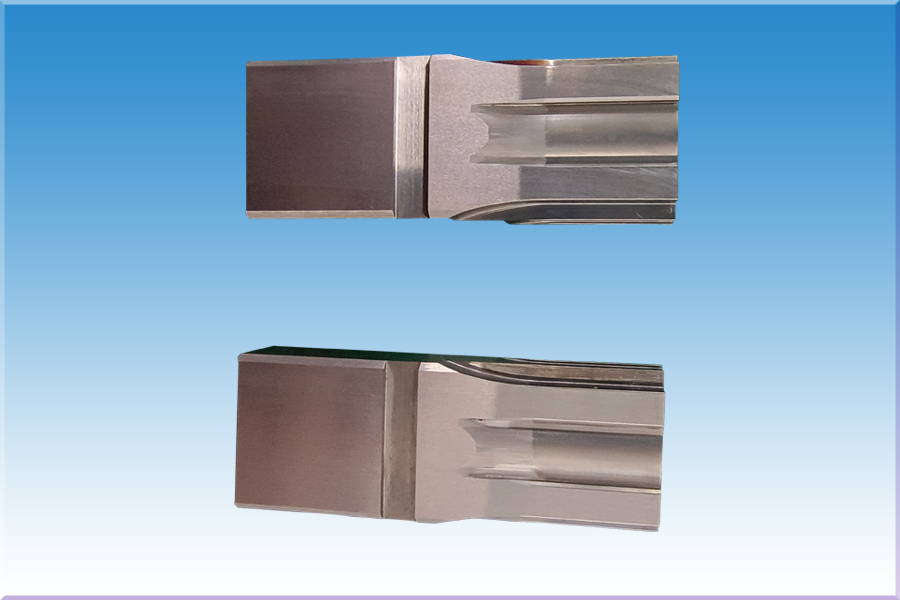
Application: The carbide punches are mostly applied in the microeconomics industry, car industry, and medical industry, the microeconomics industry includes connector and terminal sub-industry, semi-conductor sub-industry, and computer sub-industry etc.
It’s worth noting that making carbide punches requires specialized equipment and expertise. So unless you have experience with carbide machining, it may be more practical to purchase pre-made carbide punches or custom-made carbide punches from a professional and reputable supplier.
If you have any questions and would like to discuss the carbide punches, welcome to contact us at +86-15338374626, sales@langdi-precision.com.